Instalaciones hidráulicas
Los sistemas hidráulicos se
instalan para hacer el trabajo pesado en una gran variedad de vehículos y
maquinaria de producción. El fluido hidráulico a presión puede soportar
enormes cargas y circuitos relativamente pequeños pueden levantar y
mover muchas toneladas de material. Este sistema se utiliza también para
las máquinas de hacer trabajos de estampado, prensado y laminado, como
en una fábrica de acero o planta de fabricación. Los circuitos
hidráulicos también se utilizan en los automóviles, camiones y aviones
para accionar varios sistemas, tales como frenos, ascensores y
superficies de control (flaps).
Los fundamentos de la hidráulica se basan en dos principios fundamentales de la física, a saber:
• Principio de Pascal: el cual expresa que
la presión que ejerce un fluido incompresible y en equilibrio dentro de
un recipiente de paredes indeformables se transmite con igual
intensidad en todas las direcciones y en todos los puntos del fluido.
• Principio de Bernoulli: expone que en un
fluido ideal (sin viscosidad ni rozamiento) en régimen de circulación
por un conducto cerrado, la energía que posee el fluido permanece
constante a lo largo de su recorrido.
La energía de un fluido en cualquier momento
consta de tres componentes: cinética (que es la energía debida a la
velocidad que posee el fluido), potencial o gravitacional (que es la
energía debido a la altitud del fluido), y una energía que podríamos
llamar de "flujo" (que es la energía que un fluido contiene debido a su
presión).
En la siguiente ecuación, conocida como "Ecuación de Bernoulli" expresa matemáticamente este concepto:
v2·ρ
|
|
+ P + ρ·g·z = constante
|
|
2
|
siendo,
v la velocidad del fluido en la sección considerada;
ρ la densidad del fluido;
P es la presión del fluido a lo largo de la línea de flujo;
g la acelaración de la gravedad;
z la altura en la dirección de la gravedad desde una cota de referencia.
Los sistemas hidráulicos, objeto de estudio de este
tutorial, constituyen una de las formas tecnológicas que actualmente
empleamos para la transmisión de potencia en máquinas. Todo sistema
hidráulico está compuesto de los siguientes elementos principales:

- Un depósito acumulador del fluido hidráulico;
- Una bomba impulsora, que aspirando el fluido desde el depósito crea el flujo en el circuito hidráulico;
- Válvula de control que permite controlar la dirección de movimiento del fluido;
- Actuador o pistón hidráulico, que puede ser de simple o doble efecto, siendo el elemento que transmite la fuerza final;
- Red de conductos por el que circula el fluido desde la bomba hasta los actuadores y retorna al depósito acumulador;
- Filtros de limpieza del fluido hidráulico;
- Válvula de alivio, que proporciona una salida al
sistema en caso de producirse un aumento excesivo de la presión del
fluido dentro del circuito.
1.2- Ventajas e inconvenientes
A continuación se exponen algunas ventajas e
inconvenientes de los sistemas hidráulicos frente a otros sistemas
convencionales de transmisión de potencia:
a) Ventajas:
• Los sistemas hidráulicos permiten desarrollar elevados ratios de fuerza con el empleo de sistemas muy compactos.
• Permiten la regulación continua de las fuerzas que se transmiten, no existiendo riesgo de calentamiento por sobrecargas.
• Son elementos muy flexibles y que pueden
adaptarse a cualquier geometría, gracias a la flexibilidad de los
conductos que conducen el aceite hidráulico hasta los actuadores.
• Los actuadores o cilindros hidráulicos
son elementos reversibles, que pueden actuar en uno u otro sentido y que
además permiten su frenada en marcha. Además son elementos seguros,
haciendo posible su enclavamiento en caso de producirse una avería o
fuga del fluido hidráulico.
b) Inconvenientes:
• La baja velocidad de accionamiento de los actuadores o pistones hidráulicos.
• La alta presión de trabajo exige labores de mantenimiento preventivos (vigilancia de posibles fugas en las juntas).
• Sistema no muy limpio, debido a la presencia de aceites o fluidos hidráulicos.
• En general, es un sistema más caro que otros, por ejemplo los sistemas de aire comprimido.
2- Componentes del sistema
2.1- Fluido hidráulico
Para que un fluido pueda ser empleado como líquido del
circuito de un sistema hidráulico, éste deberá presentar las siguientes
propiedades:
• Ser un fluido incompresible para un rango amplio de presiones;
• Ofrecer una buena capacidad de lubricación en metales y gomas;
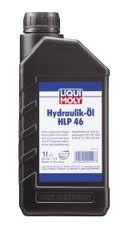
• Buena viscosidad con un alto punto de
ebullición y bajo punto de congelación (el rango de trabajo debe oscilar
entre -70ºC hasta +80ºC);
• Presentar un punto de autoignición superior, al menos a los 100ºC;
• No ser inflamable;
• Ser químicamente inerte y no corrosivo;
• Ser un buen disipador de calor, al funcionar también como refrigerante del sistema;
• Presentar buenas condiciones en cuanto a su almacenamiento y manipulación.
Los fluidos hidráulicos presentes en el mercado se pueden agrupar, en general, en tres grandes grupos:
• 1- Fluidos sintéticos de base acuosa: son resistentes a la inflamación. A su vez, se subdividen en dos tipos:
- Emulsiones de agua y aceite. En este tipo de
fluidos, además del aceite de base mineral emulsionable se emplean
aditivos que le confieren propiedades antioxidantes, antidesgaste, etc.
- Soluciones de agua-glicol. Mezclas de 40% glicol y 60% agua, más aditivos especiales.
• 2- Fluidos sintéticos no acuosos: son
compuestos sintéticos orgánicos (fosfatos ésteres simples o clorados,
hidrocarburos clorados y silicatos ésteres). Son caros, pero presentan
un punto de inflamación muy alto.
• 3- Aceites minerales o sintéticos: son
hidrocarburos extraídos del petróleo a los que se le añaden aditivos
químicos, que les confiere unas buenas prestaciones a un coste
relativamente bajo. Son los más usados comercialmente.
La forma de denominar a los fluidos hidráulicos está
regulada según la norma DIN 51524 y 51525. Así, los fluidos hidráulicos
siguiendo esta normativa se denominan todos con la letra H a la
que se le añaden otras letras, para indicar el tipo de aditivos o
propiedades del fluido. A continuación, se muestra la designación de los
fluidos hidráulicos según su tipo:
• Aceites minerales o sintéticos:
- HH: si se trata de un aceite mineral sin aditivos;
- HL: si se trata de un aceite mineral con propiedades antioxidantes y anticorrosivas;
- HP (ó HLP): aceite tipo HL con aditivos que mejoran la resistencia a cargas;
- HM (ó HLM): aceite mineral tipo HL que incluye además aditivos antidesgaste;
- HV: aceite tipo HM que además incorpora aditivos que mejoran su índice de viscosidad.
En ocasiones, a las siglas anteriores se les agrega un
número que indica el coeficiente de viscosidad según DIN 51517
(clasificación de viscosidad según ISO). Ejemplo, HLP 68, que indica:
H: se trata de aceite hidráulico;
L: con aditivos para protección anticorrosivas, con propiedades antioxidantes;
P: posee aditivos que mejora la carga;
68: código de viscosidad, según DIN 51517.
• Fluidos sintéticos de base acuosa:
- HFA: emulsión de aceite en agua (contenido de agua: 80-98%);
- HFB: emulsión de agua en aceite (contenido de agua: 40%);
- HFC: solución de poliglicoles (contenido de agua: 35-55%);
- HFD: líquidos anhídricos (contenido de agua: 0-0,1%).
• Fluidos sintéticos no acuosos:
- HFD-R: aceite a base de esterfosfatos;
- HFD-S: aceite a base de hidrocarburos halogenados;
- HFD-T: aceite a base de mezcla de los anteriores.
Por otro lado, la propiedad que más distingue un
fluido hidráulico de otro es la medida de su viscosidad. La norma DIN
51524 define los siguientes grados para la llamada viscosidad
cinemática, según la tabla siguiente:
ISO
Grados de viscosidad |
Viscosidad cinemática (mm2/s) a 40 ºC
|
|
Mín.
|
Máx.
|
|
ISO VG 10
|
9,0
|
11,0
|
ISO VG 22
|
19,8
|
24,2
|
ISO VG 32
|
28,8
|
35,2
|
ISO VG 46
|
41,4
|
50,6
|
ISO VG 68
|
61,2
|
74,8
|
ISP VG 100
|
90,0
|
110,0
|
Tabla 1. Grados de viscosidad ISO
Decir que la viscosidad cinemática es el cociente
entre la viscosidad absoluta y la densidad del fluido. En el S.I. su
unidad es el m2/s, mientras que en el sistema C.G.S. su unidad es el cm2/s, que se denomina stokes (St).
Por otro lado, la unidad en el S.I. de la viscosidad dinámica o absoluta es el kg/(m·s) ó Pa·s. En el sistema C.G.S., la unidad de la viscosidad absoluta es g/(cm·s), que se denomina poise (P).
La viscosidad del aceite lubricante se expresa con un
número SAE, definido por la Society of Automotive Engineers. Los números
SAE están definidos como: 5W, 10W, 20W, 30W, 40W, etc. En la siguiente
tabla se indica la correlación SAE-ISO:
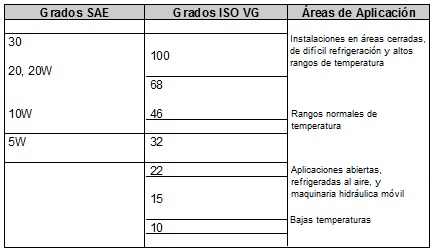
Tabla 2. Correlación entre grados de viscosidad SAE-ISO
Todos los aceites lubricantes se adelgazan cuando su
temperatura aumenta y por el contrario, se espesan cuando su temperatura
disminuye. Si la viscosidad de un aceite lubricante es muy baja, habrá
un excesivo escape por las juntas y los sellos. Si la viscosidad del
aceite lubricante es muy alta, el aceite tiende a "pegarse" y se
necesitará mayor fuerza para bombearlo a través del sistema. Se adjunta
una tabla con los rangos permitidos de viscosidad para los fluidos
hidráulicos.
Viscosidad cinemática (mm2/s)
|
|
Límite inferior
|
10
|
Rango ideal de viscosidad
|
de 15 a 100
|
Límite superior
|
750
|
Tabla 3. Rango de valores de la viscosidad cinemática
2.2- Depósito hidráulico
El depósito o también llamado tanque hidráulico, cumple con varias funciones:
- Además de servir, como uso más inmediato, de
dispositivo por donde se realiza el llenado y vaciado de fluido
hidráulico, sirve también como depósito pulmón desde donde se realiza la
aspiración por parte de la bomba.
- Sirve también como elemento disipador de calor a
través de las paredes del tanque, refrigerando así el aceite contenido
en su interior. Para ello, es necesario que el aceite tenga un tiempo de
residencia mínimo en el interior del tanque de al menos 1 ó 2 minutos.
Así en función del caudal de la bomba, se podría diseñar el volumen del
tanque. En efecto, para una bomba con un caudal de diseño, por ejemplo,
de 10 l/min, haría falta un tanque con capacidad de al menos 20 litros.
- Al servir como depósito de remanso del aceite, se
usa también para la deposición en el fondo de partículas y contaminantes
que se puedan arrastrar del circuito hidráulico, evitándose así que
vuelvan a recircular.
- Además, para aumentar el tiempo de residencia del
aceite en el tanque, se colocan en su interior unos deflectores que
sirven para dirigir la circulación del aceite por el interior del
tanque. Con ello se consigue mayor tiempo de estancia del aceite en el
depósito, y da lugar para que los contaminantes se depositen en el fondo
del tanque, además de favorecer la evaporación del agua que pueda
contener el aceite disuelto y la separación del aire.
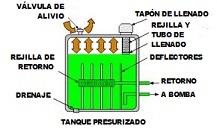
Para un circuito hidráulico se pueden fabricar dos tipos de tanques: presurizados y ventilados.
Los presurizados están sellados, evitándose así que
penetre la suciedad y la humedad en su interior. La presión interna que
se genera a medida que se calienta el fluido hidráulico también sirve
para empujar el aceite hacia la bomba, evitando que se produzca la
cavitación de la misma. No obstante, como medida de seguridad se debe
instalar una válvula hidráulica de alivio, que se utiliza para evitar
que se pueda alcanzar un exceso de presión a medida que el aceite se
calienta, y que pudiera exceder la seguridad del tanque.
Por otro lado, los tanques ventilados, al estar
abiertos a la atmósfera, permiten que haya compensación de presión
cuando se producen cambios en los niveles o en la temperatura del
aceite, y no necesitan de válvula de alivio.
Se adjunta la simbología ISO de los tanques hidráulicos, según el tipo:
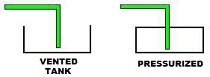
Figura 3. Esquema de representación de un tanque hidráulico
2.3- Filtros
La filtración del fluido hidráulico es necesaria para
evitar que la suciedad producida por el funcionamiento normal del
sistema termine afectando a elementos sensibles de la instalación, como
puedan ser, válvulas o la propia bomba hidráulica.
En la siguiente tabla se recogen los distintos grados de filtración exigidos, según la aplicación del sistema hidráulico.
Grados de Filtración,
en µm |
Tipo de Sistema Hidráulico
|
1-2
|
Para impurezas finas en sistemas altamente sensibles con gran fiabilidad, preferentemente en aviación y laboratorios.
|
2-5
|
Para
sistemas de mando y control sensibles y de alta presión, con
aplicaciones frecuentes en la aviación, robots industriales y máquinas
herramientas.
|
5-10
|
Para sistemas hidráulicos de alta calidad y fiabilidad, con previsible larga vida útil de sus componentes.
|
10-20
|
Para hidráulica general y sistemas hidráulicos móviles, que manejen presiones medianas y tamaños intermedios.
|
15-25
|
Para sistemas de baja presión en la industria pesada o para sistemas de vida útil limitada.
|
20-40
|
Para sistemas de baja presión con holguras grandes.
|
Tabla 4. Grados de filtración y aplicaciones
Cualquier filtro estará compuesto de una carcasa
exterior o envolvente, que contendrá en su interior el material
filtrante. Adicionalmente, dispondrá de una válvula de by-pass, tipo
antirretorno, que se abrirá cuando el material filtrante esté colmado,
de manera que permita un by-pass o paso del flujo del fluido hidráulico
evitando así que el circuito se colpase por culpa del atasco en el
filtro.
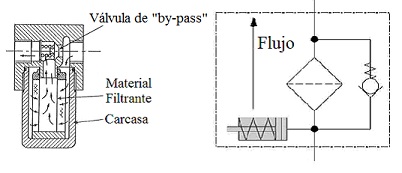
Figura 4. Esquema y símbolo de filtro hidráulico
Un filtro puede ocupar diversas posiciones dentro del
circuito hidráulico, ofreciendo prestaciones muy diversas según se
explica a continuación:
• Filtro situado en la aspiración de la
bomba: es la mejor posición si lo que se pretende es proteger a la
bomba. No obstante, aumenta el riesgo que se produzca cavitación en su
aspiración debido a la pérdida de carga que se origina en el fluido por
su paso por el filtro. Por ello, si se coloca el filtro en esta
posición, éste debe ser de un tipo que ofrezca poca pérdida de carga
localizada, como puedan ser los de tipo de mallas metálicas y los
filtros de superficie con huecos de tamaño grande. Evidentemente, esto
se traduce que el grado de filtración conseguida no sea muy buena. El
tamaño de las partículas filtradas colocando el filtro en esta posición
son relativamente grandes, encontrándose en el rango de los 50 a 100 µm.
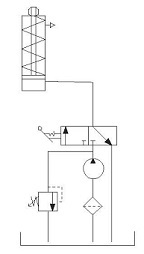
Figura 5. Filtrado en la aspiración
• Filtro situado en el conducto de
impulsión: dada su situación, en la salida de la bomba, se sitúa en la
línea de alta presión. Esto condiciona que los filtros así situados
requieran de una mayor robustez. No obstante, en esta posición se
consiguen filtrados más exigentes, estando el tamaño de las partículas
retenidas en el rango de los 10 a 25 µm.
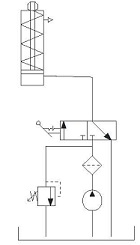
Figura 6. Filtrado en la impulsión
• Filtro en el circuito de retorno al
depósito: a diferencia de los casos anteriores, colocando el filtro en
la tubería de retorno al depósito se evitan los problemas de resistencia
a la presión, o los riesgos de cavitación en la aspiración de la bomba.
Para esta posición, el tamaño de las partículas que se consigue filtrar
se encuentra entre 25 y 30 µm.
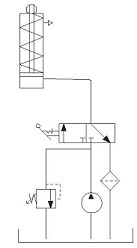
Figura 7. Filtrado en el retorno
• Filtro situado en circuito independiente:
Para circuitos con altas exigencias, el filtro se puede situar en un
circuito independiente que también realice labores de refrigeración del
fluido hidráulico.
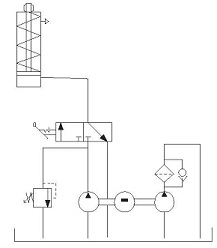
Figura 8. Filtrado en circuito independiente
A continuación se incluye una tabla donde se indican
los grados de filtración y la posición recomendada para situar el
filtro, según el tipo de componente o elemento hidráulico considerado.
Elemento hidráulico
|
Posición recomendada del filtro
|
Grado de filtración,
en µm |
Bomba de émbolos axiales
|
Línea de retorno y/o línea de presión
|
≤ 25
|
Línea de baja presión
|
≤ 25
|
|
Bombas de engranajes y émbolos radiales
|
Línea de retorno
|
≤ 63
|
Válvulas distribuidoras, de presión, de caudal y cierre; cilindros
|
Línea de aspiración
|
≤ 63
|
Motores hidráulicos
|
Línea de retorno
|
≤ 25
|
Tabla 5. Grados de filtración y posiciones del filtro
2.4- Bomba hidráulica
La bomba hidráulica es el componente que genera el
flujo dentro del circuito hidráulico, y está definida por la capacidad
de caudal que es capaz de generar, como ejemplo, galones por minuto,
litros por minuto, o centímetros cúbicos por revolución. Hay dos grandes
grupos de bombas: rotativas y alternativas.
A) Bombas rotativas:
Dentro de la familia de bombas rotativas, se encuentran los siguientes tipos:
• Bombas de engranajes: Las bombas de
engranajes son compactas, relativamente económicas y tienen pocas piezas
móviles, lo que les confiere tener un buen rendimiento.
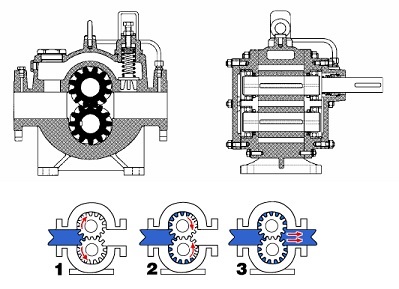
Figura 9. Bomba de engranaje. Principio de funcionamiento
La cilindrada (V) de una bomba de engranaje se obtiene a partir de la siguiente expresión:
π
|
||
V =
|
· (De2 - Di2) · A
|
|
4
|
siendo, De y Di los diámetros de punta y de base del diente del engranaje y A es el ancho de la carcasa de la bomba.
• Bombas lobulares: son bastante semejantes
a las de engranajes, pero con un número de dientes menor y con rangos
de funcionamiento menores. Normalmente se utilizan para incrementos de
presiones bajas donde puede haber problemas de erosión en los dientes si
se empleara una bomba de engranajes.
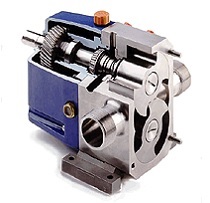
Figura 10. Bomba hidráulica de tipo lobular
• Bombas de paletas: básicamente constan de
un rotor, paletas deslizantes y una carcasa. Se dividen en dos grandes
tipos, compensadas y no compensadas.
En las bombas de paletas no compensadas cuando el
rotor gira desplaza las paletas hacia fuera debido a la fuerza
centrífuga, haciendo contacto con el anillo, o la carcasa, por lo que se
forma un sello positivo. El fluido en este tipo de bombas entra y va
llenando la porción de volumen mayor que se genera con el hueco dejado
por el rotor descentrado dentro de la carcasa. Al girar entonces se
genera una fuerza que empuja el fluido hacia afuera. Se denominan de
paletas no compensadas porque una mitad del mecanismo de bombeo se
encuentra a una presión inferior a la atmosférica, mientras que la otra
mitad estará sometida a la presión de trabajo propia del sistema.
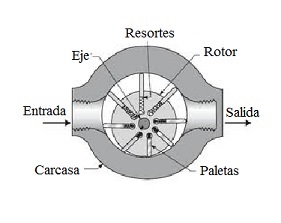
Figura 11. Esquema de una bomba de paletas
Para equilibrar los esfuerzos dentro de la bomba se
desarrollaron las llamadas bombas de paletas compensadas. En este tipo
se cambia la forma circular de la carcasa por otra forma geométrica en
forma de leva, que consigue equilibrar las presiones interiores.
B) Bombas hidráulicas alternativas:
• Bombas de émbolos o pistones: en este
tipo de bombas se convierte el movimiento giratorio de entrada de un eje
en un movimiento de salida axial del pistón. Son un tipo de bombas por
lo general, de construcción muy robustas y adecuadas para presiones y
caudales altos. Su rendimiento volumétrico también es alto.
Se pueden distinguir tres tipos de bombas de pistones:
1. Pistones en línea: tienen una construcción muy simple y el rendimiento que son capaces de obtener puede llegar al 97%.
El cálculo de la cilindrada (V) de una bomba de pistones en línea se obtiene a partir de la siguiente expresión:
π
|
||
V =
|
· D2 · C · Z
|
|
4
|
siendo, C la carrera del pistón, D es el diámetro de cada pistón y Z es el número de pistones.
2. Bombas de pistones radiales: en este tipo se
puede también regular el caudal de cada pistón. Su cilindrada puede ser
fija o variable, y el rendimiento puede llegar a ser de un 99 %.
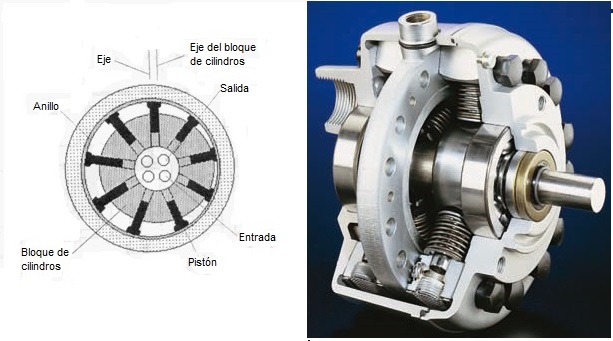
Bomba de pistones radiales
El cálculo de la cilindrada (V) de una bomba de pistones radiales se obtiene a partir de la siguiente expresión:
π
|
||
V =
|
· e · D2 · Z
|
|
2
|
siendo, e es la excentricidad (o doble de la carrera), D es el diámetro de cada pistón y Z es el número de pistones.
3. Bombas de pistones axiales: también pueden ser de cilindrada fija o variable. En las que son de caudal variable, pueden autorregularse.
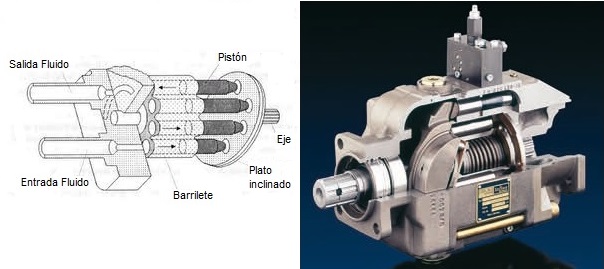
Bomba de pistones axiales
La cilindrada (V) de una bomba de pistones axiales se obtiene a partir de la siguiente expresión:
π
|
||
V =
|
· Dp2 · Z · Dm · tgβ
|
|
4
|
siendo, Dp el diámetro de cada pistón, Z es el número de pistones, Dm el diámetro de la máquina y β
es el ángulo de inclinación del eje (que puede ser fijo si la máquina
es de eje recto, o variable si se trata de una máquina con sistema de
inclinación del eje).
• Bombas de diafragma: en este tipo de
bombas el flujo se consigue por el empuje de unas paredes elásticas, de
membrana o diafragma, que varían el volumen de la cámara, aumentándolo y
disminuyéndolo alternativamente.
En la siguiente tabla se resumen los distintos rangos de trabajo de algunos de los tipos de bombas hidráulicas más empleadas:
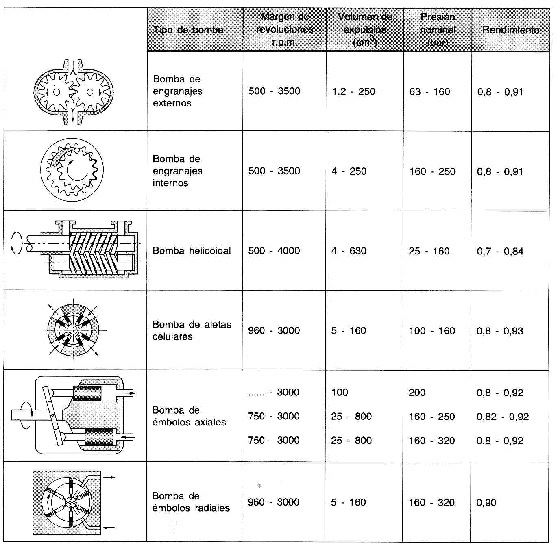
Tabla 6. Rangos de trabajos para las bombas hidráulicas
2.5- Cilindro actuador
El cilindro actuador es el elemento final que
transmite la energía mecánica o empuje a la carga que se desee mover o
desplazar. Aunque hay actuadores de tipo rotativo, los más conocidos son
los cilindros lineales.
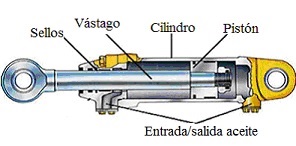
Los cilindros lineales pueden ser de simple o de doble
efecto. En los cilindros de simple efecto el aceite entra sólo por un
lado del émbolo, por lo que sólo puede transmitir esfuerzo en un
sentido. El retroceso se consigue o bien por el peso propio del
cilindro, bien por la acción de un muelle o por una fuerza exterior
(ejemplo, la propia carga que se eleva). Por el contrario, en los
cilindros de doble efecto, el aceite puede entrar por los dos lados del
émbolo, por lo que puede transmitir esfuerzo en los dos sentidos del
movimiento.
Uno de los aspectos a tener en cuenta en el diseño de
un cilindro hidráulico es cómo realizar el amortiguamiento o frenada del
movimiento del vástago, cuando éste se acerca al final de carrera,
evitando así que se produzcan impactos entre el pistón interior y la
tapa del cilindro.
Para ello los cilindros hidráulicos disponen de un
pivote amortiguador que paulatinamente reduce la salida del aceite hasta
que, poco antes de llegar al final de carrera, cierra totalmente el
paso del caudal de salida del aceite, "bypasseando" el flujo mediante
una válvula de estrangulamiento por donde se evacua el resto del aceite.
De este modo se va disminuyendo progresivamente la velocidad del
cilindro y el pistón se consigue frenar suavemente. Este tipo de
amortiguamiento para las posiciones finales de carrera se utiliza si las
velocidades del cilindro oscilan entre 6 m/min y 20 m/min.
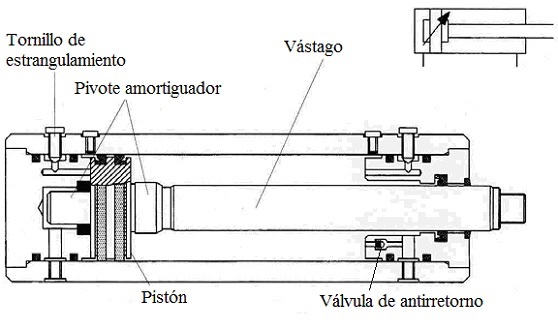
Figura 13. Amortiguamiento del cilindro en final de carrera
Por último, cabe indicar un aspecto a tener muy en
cuenta en el diseño de los cilindros hidráulicos, y en concreto, en lo
que se refiere al vástago.
En efecto, cualquier pieza esbelta sometida a
esfuerzos de compresión, y el vástago estará sometido a este tipo de
solicitación, corre el riesgo de sufrir el fenómeno de pandeo. Para
tener en cuenta este tipo de inestabilidad, el cálculo del diámetro del
vástago se realiza aplicando la Teoría de Euler. Según esta teoría, para
un determinado diámetro (d) de vástago, la fuerza máxima que puede soportar sin que sufra de pandeo viene dada por la siguiente expresión:
K
|
|
F =
|
|
S
|
donde S es un factor de seguridad de valor 3,5 y K es la carga de pandeo (en kg) que se calcula mediante la siguiente expresión:
π2 · E · I
|
|
K =
|
|
L2
|
donde,
E es el módulo de elasticidad, de valor 2,1·106 kg/cm2 para el acero;
I es el momento de inercia de la sección trasversal del vástago, de valor π·d2/64 para un vástago de sección circular de diámetro d;
L es la longitud de pandeo del vástago, que depende del método de sujeción empleado en su montaje.
La longitud de pandeo L, en general no va a
coincidir con la longitud real del vástago, sino que va a depender, como
ya se ha dicho de la forma en que se haya realizado el montaje del
cilindro.
En la siguiente tabla se indica cómo se calcula L en función de las distintas situaciones de montaje del cilindro hidráulico.
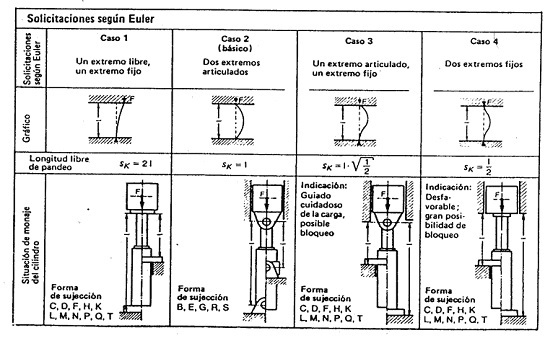
Tabla 7. Cálculo de la longitud libre de pandeo, L
2.6- Tuberías hidráulicas
Para la conducción del fluido hidráulico se emplean
tanto tuberías rígidas de acero sin soldadura, como mangueras flexibles,
evitándose en todo momento emplear elementos galvanizados, dado que el
zinc presente puede ser muy reactivo con ciertos aditivos presentes en
los fluidos hidráulicos.
No hay comentarios:
Publicar un comentario